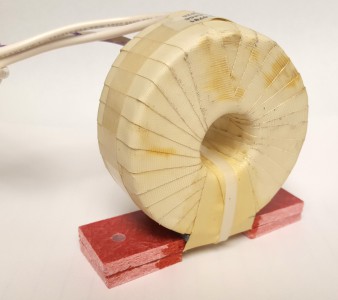
Power inductors are important electronic components used in different electrical applications. They are designed to store energy and ensure low core losses which allows for efficient power conversion. However, designing an inductor is not an easy task. There are a variety of factors to consider in the design process. In this post, we provide five important tips that you can use to enhance inductor design.
5 Power Inductor Design Tips
The following tips are connected with certain requirements which need to be factored in when creating or choosing a power inductor. Hence, each tip will help provide a solution on how to enhance that particular requirement.
- Switching Frequency: Generally, Integrated Circuits (ICs) that are found in the market have a switching frequency from 20 kHz to 2MHz. Compared this to some regulators that only have a switching frequency range of 30 to 55 kHz.
Tip: To ensure high switching frequency levels, you can try using certain types of inductor materials:
- Utilize materials such as ferrite, powdered iron and specialty iron alloyed powders (such as Superflux) to ensure that the frequency required can be met.
- If you require the switching frequency to be between 100 and 1000 kHz then using both powdered iron and ferrite materials are an option.
- For switching frequencies greater than 1000 kHz specialty iron alloyed powders and ferrite materials are the best option.
- Inductance Value: The goal of using an inductor is to reduce the amount of power loss in an application. The inductor value is an important factor, as it is connected with the ripple current, the unwanted residual DC current output. The ripple current is essential to understanding the core losses. Hence, you should keep in mind:
Tip:
- When the ripple current is smaller, the inductance value will be higher.
- When the ripple current is higher, the inductance value will be lower.
By understanding the connection between the inductance value and the ripple current, you will be in a better position to minimize power losses.
- Inductor Current Ratings: Some manufacturers provide simulation software along with inductors. This software allows the client to calculate the inductor loads. They can calculate the ripple current load, as well as the DC current load. However, the data can be misinterpreted.
Tip: Power inductors are known to have self-heating DC currents, which are generally above 104oF. The saturation current is often said to be when the inductance value falls by 10%. However, this is not a standard accepted value in data sheets, which leads to misinterpretation. Hence, take care to understand the data sheet specifications.
- DC Resistance: DC resistance is essential in determining the wire heating losses. It is important to find a power inductor with the least amount of resistance. However, many applications require small sized inductors which require smaller diameter wires. These smaller gauge wires increase resistance. Trade offs must be made to minimize resistance and yet retain power storage capabilities.
Tip: If the size of the inductor is correct, then:
- Low DC resistance will be achieved with minimal rise in temperature.
- High inductances often require other conductor materials
- Inductor Type: Many times un-shielded power inductors can cause problems when the windings magnetically couple with neighboring components and conductor traces. To prevent this:
Tip: Use a magnetically shielded power inductor. Also, insure that the design does not have circuit boards above the component or any traces under the components. This will help prevent magnetic coupling by placing an air gap between the components.
These five tips are simple but can help ensure that proper and long-lasting performance of power inductors. If you have any questions regarding this, the best thing to do is contact Custom Coils.