Toroidal transformers are widely used for industrial power transmission applications. These transformers get their name from the toroidal core that resembles a donut-shaped or torus core. The secondary and primary windings of the transformer are wound across the surface of the torus core. These windings are separated by an insulating material. The construction of this core helps minimize the leakage of magnetic flux. Understanding these transformers can be difficult because they are used differently across systems. This post aims to answer all the questions that you may have in mind regarding these transformers
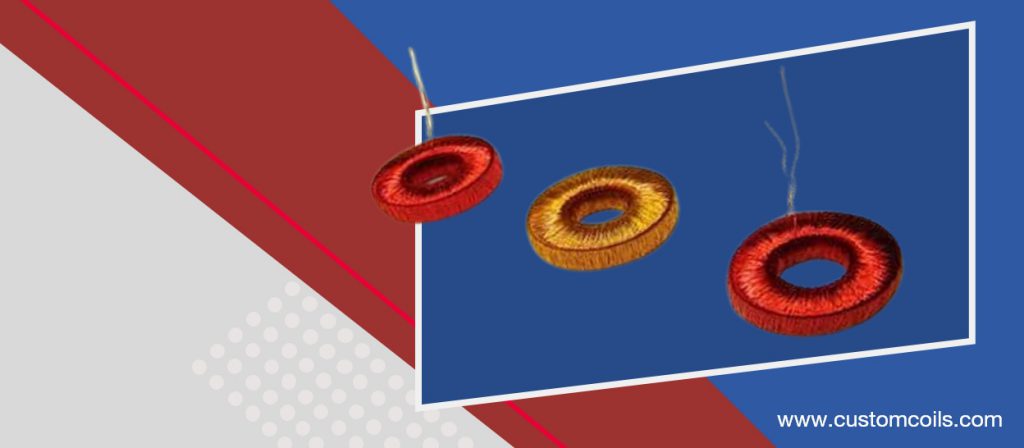
What are the causes of vibration in toroidal transformers?
Toroidal transformers may experience vibrations due to any of the following reasons:
- The transformer is overloaded.
- The current design of the transformer cannot match the parameters of the load.
- The fixing and installation of the transformer is quite loose.
- The input voltage of the transformer is 10% more than its rated value.
What are the different types of toroidal transformer configurations?
The configuration refers to the input voltages the transformer accepts and the number of leads and windings the transformer contains.
The transformers are available in three configurations.
- Single Configuration: These transformers feature a primary coil winding and are designed for receiving a single input voltage.
- 5-lead Transformers: These transformers generally use 3 leads as the primary that is center-tapped and 2 leads as the output voltage.
- Dual Configuration: As the name suggests, the transformers can accept two different voltages. They feature two primary coils with two windings and can easily accept two voltages. It is always recommended to use these transformers with a two-lead voltage selector for switching input voltages.
What are the advantages of choosing toroidal transformers over other types of transformers?
There are several advantages of choosing toroidal transformers over other industrial transformers. The following are a few common ones among them.
- Near Ideal Design: This means no leakage of magnetic flux. The magnetic flux is contained within the windings. The windings are equally distributed over the toroidal core, which minimizes the scope of magnetic flux leakage. The magnetic flux is utilized to couple secondary and primary windings.
- Electromagnetic Shielding: The geometry of the toroidal core creates less EMI and functions better around sensitive components, thereby protecting them from electromagnetic interference. This characteristic makes toroidal transformers ideal for applications where sensitive components may be involved.
- High Transformer Efficiencies: This is the ratio of the transformer’s output power of the secondary windings to the input power of primary windings. Generally, toroidal transformers are known for higher power efficiency than other types. This can be sometimes as high as 99%.
- No Noise and Fringing: Toroidal cores are often confused with solenoid cores. Solenoid cores feature three air gaps through which the magnetic flux leaks and affects the other components. However, the toroidal cores possess consistent construction and feature no air gap. This minimizes the chances of magnetic flux spreading, also known as fringing. The absence of air gap also minimizes noise.
- Compact Construction: If you match by size, then you will realize that toroidal transformers are smaller than many other types of transformers you may have used. This is due to its near perfect construction. The core is utilized to its entirety. Unlike UI and EI cores, no return paths are used for the magnetic flux. This makes the construction smaller.
- Low Signal Distortion: Low magnetic flux leakage means low signal distortion. Leaked magnetic flux can produce stray currents when their magnetic lines cross nearby conductors. This leads to the mixing of unwanted signals with sensitive signals, thereby inducing distortion. Due to low power distortion, the toroidal transformers are regularly used in applications where high signal resolution may be needed.
- Minimal Heat Generation: High efficiency of toroidal transformers helps reduce heat generation. If you have seen a large transformer, there will be an oil cooler for heat dissipation; similarly, in small transformers, there will be a metal heat sink to absorb the heat. However, toroidal transformers are more efficient at heat dissipation and reduce the temperature rise of the transformer even if it is subjected to high loads.
- Low Transformer Noise: Noise in a transformer is generally due to high mechanical humming of the core. Sometimes, the core material vibrates, affecting the adjacent parts. Core vibration can be more realized in transformers that feature loose components. With toroidal transformers, the chances of core humming is quite low because the design is consistent. There are no air gaps between yokes and limbs.
What are the different types of core materials used in toroidal transformers?
The following types of core materials are used for making toroidal transformers.
- Ferrite Cores: These cores are made of materials like iron oxide, metal-oxide ceramic, and are mixed with other materials like copper, cobalt, zinc, manganese, and nickel. Ferrite cores possess high resistivity and help reduce the production of eddy currents. You can choose between nickel-zinc and manganese-zinc ferrite cores.
- Laminated Iron Alloy Cores: These transformers feature metal sheets, which are stamped into the required shape. The stamped sheets are stacked with an insulating layer between them. This laminated construction help reduce the eddy currents. These cores are generally made from two types of materials – nickel-iron and silicon-iron. Most toroidal transformers are made from nickel-iron material. However, silicon-iron is used as a core material in high-power transformers.
- Amorphous Steel and Silicon Steel: Magnetic cores made of amorphous steel and silicon steel have been popular for several years now and are used in many industrial applications.
- Several layers of paper-thin metallic tapes made of amorphous steel are used to make the magnetic core. Amorphous steel cores assure fewer losses than other magnetic cores, which is why they are used in high temperature applications.
- Silicon steel material possesses low losses, high permeability, high saturation flux density and electrical resistivity. All these properties help cut down eddy current losses and make them an ideal choice for high-performance applications.
- Solid Iron and Carbonyl Iron: The cores made of solid iron offer magnetic flux and do not saturate iron, thereby helping retain high magnetic fields. Carbonyl iron is a form of pure iron that assures stability across a wide range of magnetic flux and temperatures. The cores made of carbonyl iron are known as RF cores and possess low losses and permeability. Solid iron core transformers are not recommended for AC applications because their high contained magnetic fields produce high eddy currents. These eddy currents are known to produce high heat at high frequencies
Are toroidal transformers ideal for all applications? If not, under what circumstances should they be avoided?
These transformers are ideal for most applications. However, they should be avoided in the following circumstances.
- The transformer and paired equipment parameters do not match.
- The transformer has failed to perform in certain processes and tests.
- The transformer characteristics do not match the application requirements or operational environments.
What are the important factors to consider when buying a toroidal transformer?
You need to consider different things when buying them for your application.
- Number of windings: Generally, a toroidal transformer comprises a secondary and primary winding. However, most times, the transformers are designed with one primary and two secondary windings. The secondary windings can be configured in either series or parallel manner or they can be used independently.
- Primary and Secondary Voltages: Transformers are rated for primary and secondary voltages. These voltages are usually specified together.
- Mounting: The transformer can be mounted in various ways to ensure its proper performance. The following are a few popular mounting types:
- Chip transformers are integrated circuits, which are produced using thin film technology.
- Chassis mount devices are generally screwed onto the internal framework.
- H-frame mounting helps secure and hold the transformer over a flat surface. This type of mounting is more appropriate for high shock and vibration applications.
- Power Rating: This is the capacity of the transformer to deliver or accept the power.
- Standards and Certifications: If you are working in a highly regulated industry, you must choose toroidal transformers that are compliant with industry standards like WEEE and RoHS or other widely accepted certifications like ISO, UL, CE, and IEC.
- Operating Frequency: This frequency is intended for AC applications. The frequencies vary across applications. For military and aerospace applications, the frequencies would be as high as 400 Hz, while for utility applications, it would be 50 Hz or 60 Hz.
- Losses: The transformer experiences power drop due to factors like coil and core losses. This power drop is referred to as losses, and specified in watts.
What are the common applications of toroidal transformers?
These transformers are used across industries. The following are two common applications.
- Medical Industry: High accuracy and superior efficiency are two important requirements in this industry. Both these are effectively met by toroidal transformers. They assure low current leakage and reliable performance in specified conditions. Due to their compact footprint, these transformers can be easily integrated into medical devices where the space and weight of components can be a constraint.
- Electrical Circuits: The transformers are commonly used in electronic circuits such as inverters, computers, television, amplifiers, and audio-visual applications.
If you are considering high-quality toroidal transformers for your industrial application, ensure to source them from trusted and experienced manufacturers like Custom Coils. The company makes toroidal transformers in different formats like horizontal, vertical, PC mount bobbin headers, and surface mount. They are offered with inductors up to 20 amps, current transformers, pulse transformers up to 250 KHz, and common mode choke. You can get in touch with the experts at the company to discuss your requirements.